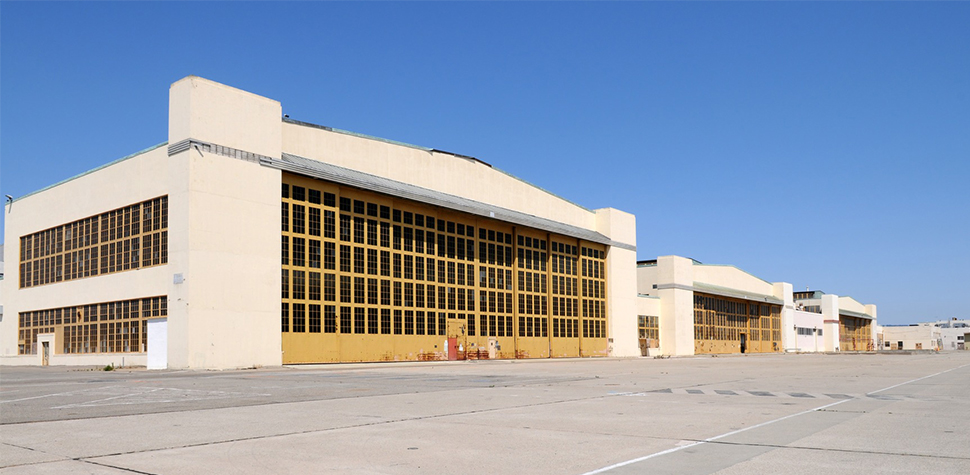
Commercial and Residential Redevelopment of a Decommissioned Military Facility
Vista Environmental Consulting (Vista) key personnel oversaw and performed hazardous materials assessments, cost estimates, remediation/demolition/deconstruction design, and remediation oversight management of all of the buildings on 215 acres at the former Fleet Industrial Supply Center (FISC) and East Housing areas of the former Alameda Naval Air Station.
This project was accomplished in preparation for the commercial and residential redevelopment of the decommissioned military facility. The buildings that were part of this project included 589 units of housing (800,000 square feet), ten warehouses (two million square feet), hospital building (120,000 square feet) and several smaller buildings including a boiler building.
Pre-assessment research, including extensive site visits and aerial photo/historical document reviews, uncovered previously missed hazardous materials including underground storage tanks (USTs), buried building debris from previous demolitions, and pesticide contaminated soil/building materials.
The hazardous materials survey portion included a detailed inventory of asbestos containing materials including subsurface piping and soil, lead-based and lead containing components, PCB ballasts and transformers, universal waste, ozone depleting chemicals, organochlorinated pesticide contaminated soil and building materials and UST identification.
A cost estimate for abatement was provided along with the survey report. Remediation design specifications and drawings that were integrated with the building demolition/deconstruction and civil infrastructure demolition design were provided for use in project bidding.
Vista’s key personnel were involved in the first phase (residential and commercial outfall) of remediation oversight of the hazardous materials found. The project team met with the community living adjacent to the property prior to abatement to discuss operations and safeguards. Noise monitoring was added to fence line asbestos and lead monitoring at the request of the community leaders.
The project team also met with the local air quality management district (AQMD) to discuss removal of weathered asbestos paneling that covered four large warehouses. The outcome of the meeting allowed to the abatement operations to be done at a lower regulatory compliance level which saved time and money. Vista’s key personnel performed air quality monitoring, observed and inspected the removal operations to insure compliance with regulatory rules and contractual obligations. In addition to this they also managed the hazardous waste manifests and documented the subsurface infrastructure when it was unearthed.
The relationship with the regulators helped the project team when damaged subsurface asbestos piping was found by the new construction general contractor. Cal/OSHA was called and the local AQMD contacted the team and brought them in to the discussions. Vista’s key personnel worked with the team to write a response to Cal/OSHA’s violation and helped reduce the amount of the fine by writing a work practice scope and training the general contractor’s personnel.